24 and 38 Wolcott Hill Road Energy Study and Design
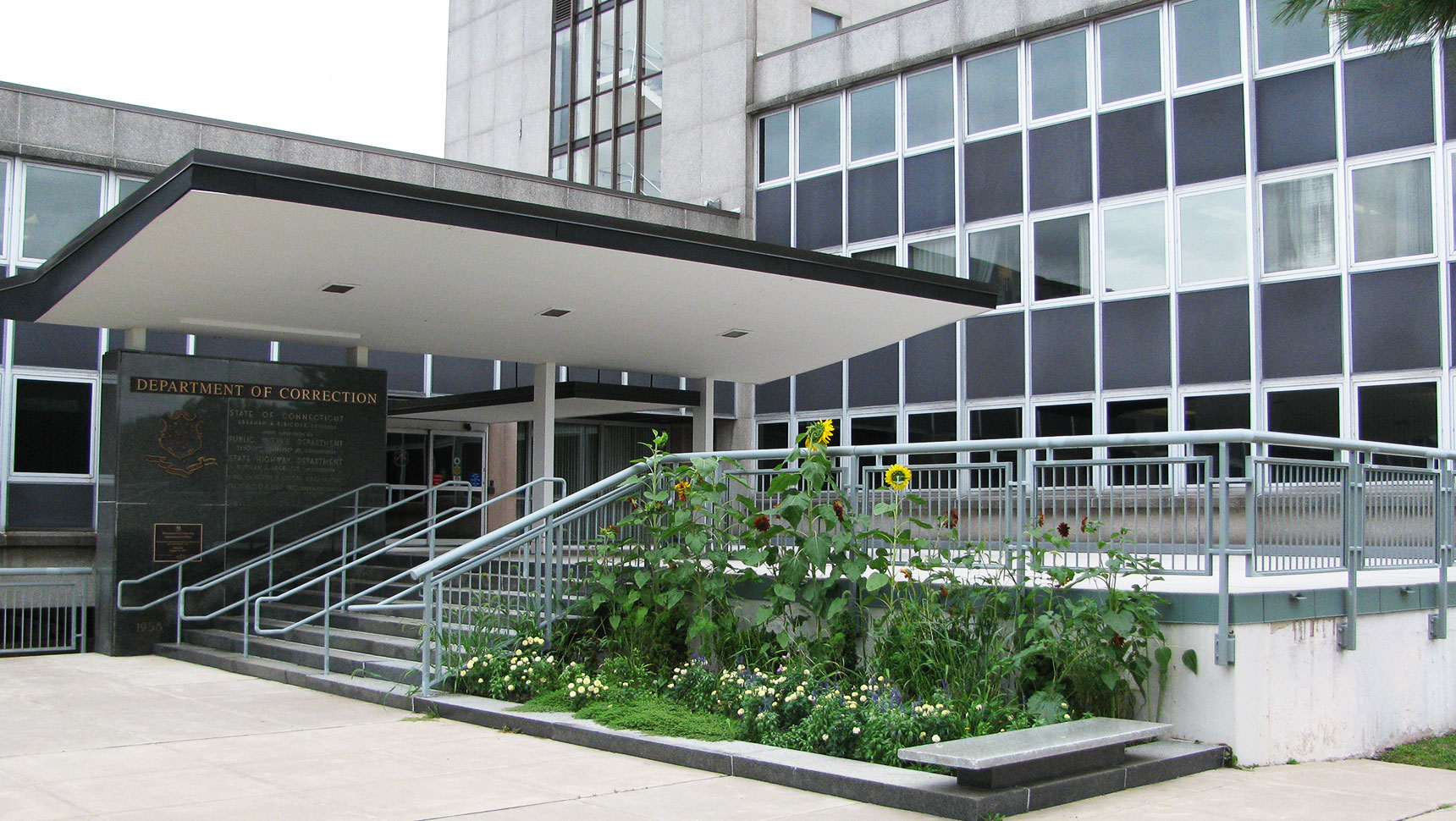
Fuss & O’Neill was contracted to provide engineering services associated with an energy improvement project at 24 and 38 Wolcott Hill Road in Wethersfield.
The first phase of this project was an energy conservation study. Fuss & O’Neill’s MEP (mechanical, electrical, and plumbing) team analyzed four energy conservation measures:
Additionally, our team determined the feasibility of:
Fuss & O’Neill’s analysis was based on review of lighting layouts, levels, and fixtures; review of HVAC systems and controls; review of the existing power plant and associated systems; and review of water savings measures for plumbing fixtures. The Energy Star rating system was used to compare the building energy performance to that of others of the same type.
We presented our findings, opinions of cost, and recommendations in a final report.
The report discussed the energy- and water-saving potential of the measures. We provided an outline of the next steps for those measures that suggested a payback in the 10-year range.
After our initial study, Fuss & O’Neill’s MEP team and structural engineers were contracted to design the energy upgrades. This required careful project management to coordinate the complexity of completing such a major project in occupied buildings that houses sensitive agencies and has high security.
These upgrades provided energy- and water-saving improvements, increasing cost savings, and resiliency efforts.
Our team provided a path for return air to the large main air handler serving the perimeter induction HVAC system in Building 24, which previously ran on 100% outside air. We designed a complex exterior return fan and duct system to capture building exhaust and return it to the main fan room air handler.
This modification was of utmost importance to the client due to the large associated energy savings.
Additionally, at the client’s request, we replaced a failed chiller in the central plant, converted certain failing pneumatic controls to BMS, rehabilitated the remaining pneumatic controls, modernized the BMS for more efficient operation, and upgraded outdated BMS.
During construction, the client encountered unexpected age-deterioration issues in parts of the existing HVAC systems. Fuss & O’Neill was able to rapidly respond to this challenge, adding this to our scope and addressing the issue without incurring significant delay.